In the world of metal fabrication, few materials offer the versatility and benefits of aluminum. Its lightweight nature, resistance to corrosion, and strength make it an ideal choice for a wide range of applications, from residential railings to industrial components. When it comes to working with aluminum, custom fabrication paired with Tungsten Inert Gas (TIG) welding emerges as the gold standard. This combination allows for the creation of high-quality, durable, and aesthetically pleasing products that meet the specific needs of various industries.
What is Custom Aluminum Fabrication?
Custom aluminum fabrication is the process of shaping, cutting, and assembling aluminum materials to create structures or products that are tailored to a client’s specifications. Unlike mass-produced items, custom fabrication is all about precision and personalization. It involves working closely with the client to understand their unique requirements and then using advanced techniques and machinery to bring their vision to life.
Key Aspects of Custom Aluminum Fabrication:
- Design and Planning:
The process begins with a thorough design phase, where detailed blueprints and CAD (Computer-Aided Design) drawings are created. This step is crucial for ensuring that every aspect of the project meets the client’s expectations, from the dimensions to the final finish. - Cutting and Shaping:
Once the design is finalized, the aluminum sheets or extrusions are cut and shaped according to the specifications. This can involve a variety of techniques, including laser cutting, water jet cutting, and CNC (Computer Numerical Control) machining. These methods allow for high precision and the ability to create complex shapes and designs. - Forming and Assembly:
After the pieces are cut, they are formed and assembled into the final product. This may involve bending, rolling, and other forming techniques to achieve the desired shape. The assembly process often requires high attention to detail, especially when working with custom designs that demand seamless integration of multiple components. - Finishing:
The final step in custom aluminum fabrication is finishing, which can include polishing, anodizing, powder coating, or painting. These finishing processes not only enhance the appearance of the aluminum but also add an extra layer of protection against environmental factors like moisture and UV radiation.
The Role of TIG Welding in Aluminum Fabrication
When it comes to joining aluminum parts together during the fabrication process, TIG welding is often the method of choice. TIG welding, or Tungsten Inert Gas welding, is a process that uses a non-consumable tungsten electrode to produce the weld. This technique is particularly well-suited for aluminum due to its ability to produce clean, strong, and precise welds without compromising the integrity of the metal.
Why TIG Welding is Ideal for Aluminum:
- Precision and Control:
TIG welding provides the welder with exceptional control over the welding process, allowing for precise and clean welds. This is especially important in custom fabrication, where the final product must meet exacting standards. - Clean Welds:
One of the standout features of TIG welding is the ability to produce welds with minimal contamination. Since aluminum is prone to oxidation, the use of an inert gas (usually argon) in TIG welding prevents contamination and ensures a clean, strong weld. - Strong, Durable Joints:
The strength of a weld is crucial in any fabrication process. TIG welding creates robust, durable joints that can withstand significant stress and strain, making it ideal for both structural and aesthetic applications. - Versatility:
TIG welding can be used to weld a variety of metals, including aluminum, stainless steel, and even more exotic materials. This versatility makes it a go-to technique for custom fabrication projects that may involve multiple types of metals.
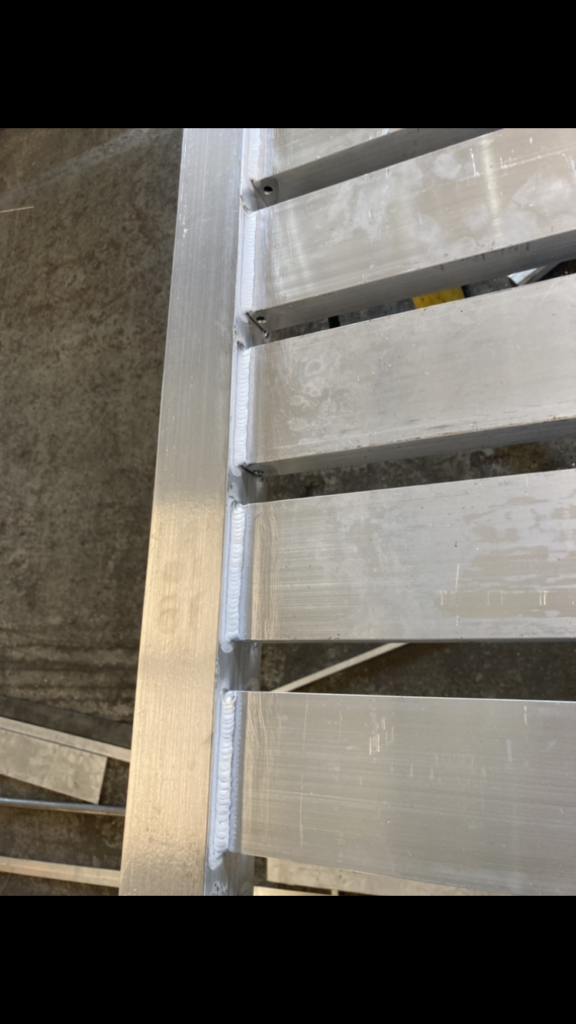
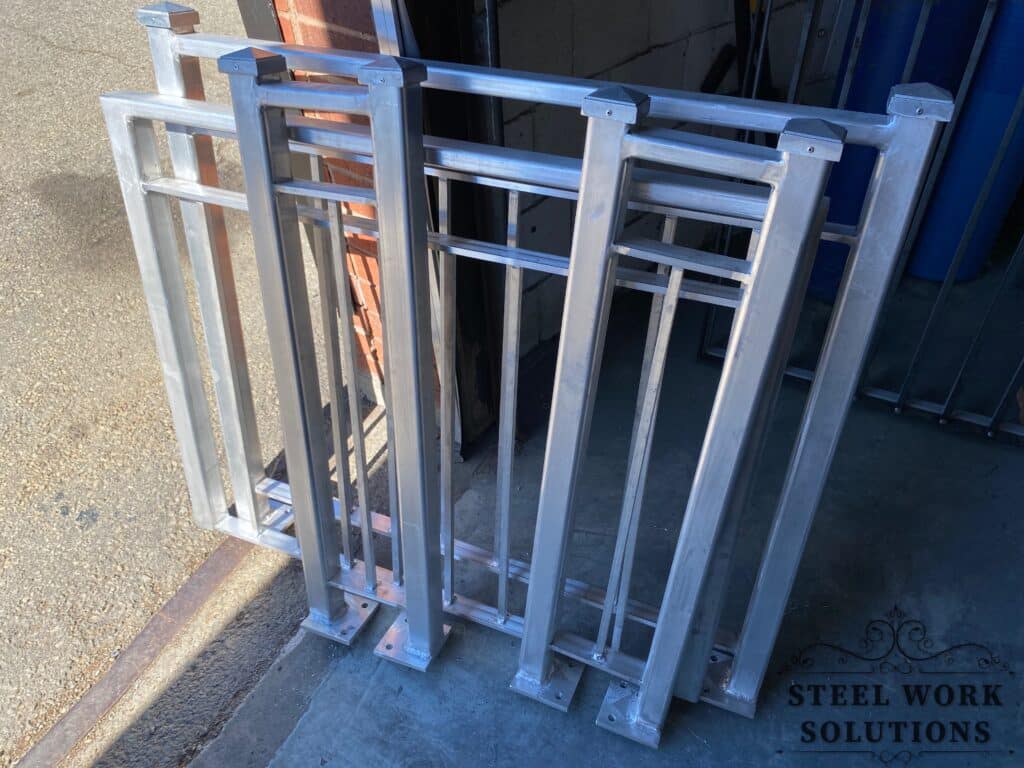
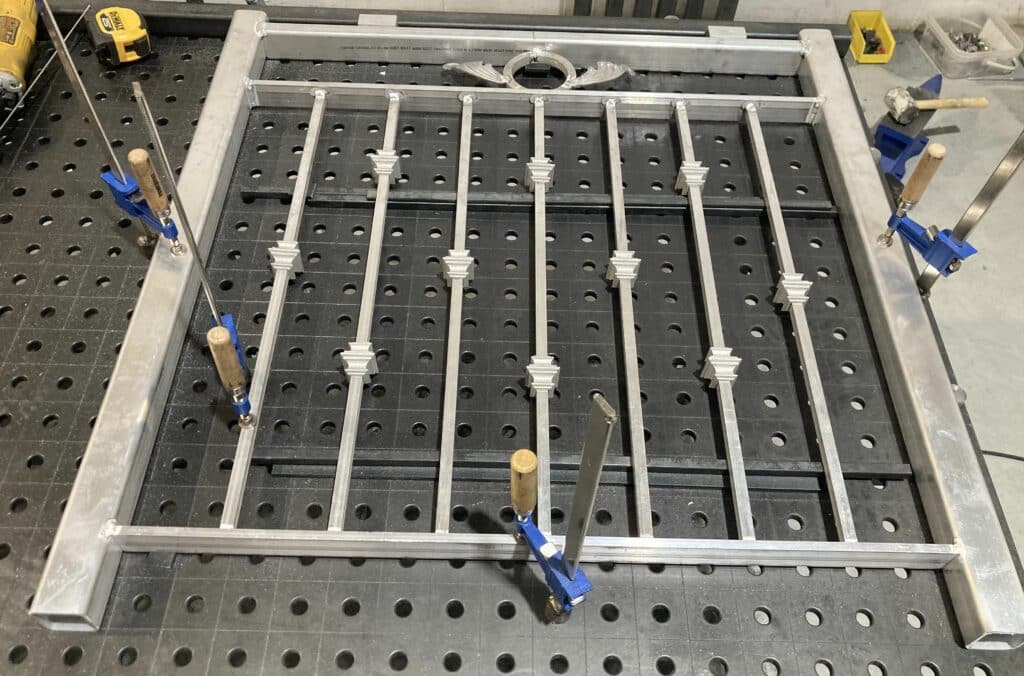
Applications of Custom Aluminum Fabrication and TIG Welding
The combination of custom aluminum fabrication and TIG welding is used in a wide range of industries and applications. Here are some of the most common:
1. Residential and Commercial Railings:
Custom aluminum railings are a popular choice for both residential and commercial properties due to their durability, low maintenance, and aesthetic appeal. TIG welding ensures that these railings are not only beautiful but also strong enough to provide safety and support.
2. Automotive and Aerospace Components:
The lightweight nature of aluminum makes it an ideal material for automotive and aerospace parts. Custom fabrication allows for the creation of parts that are tailored to the specific needs of each vehicle or aircraft, while TIG welding ensures that these parts are securely and precisely assembled.
3. Architectural Features:
From modern facades to intricate architectural details, custom aluminum fabrication allows for the creation of unique and visually striking features. TIG welding plays a critical role in ensuring that these elements are seamlessly integrated into the overall design.
4. Industrial Equipment:
In industrial settings, custom aluminum fabrication is often used to create equipment and machinery that are resistant to corrosion and capable of withstanding harsh environments. TIG welding ensures that these components are strong and reliable, even under extreme conditions.
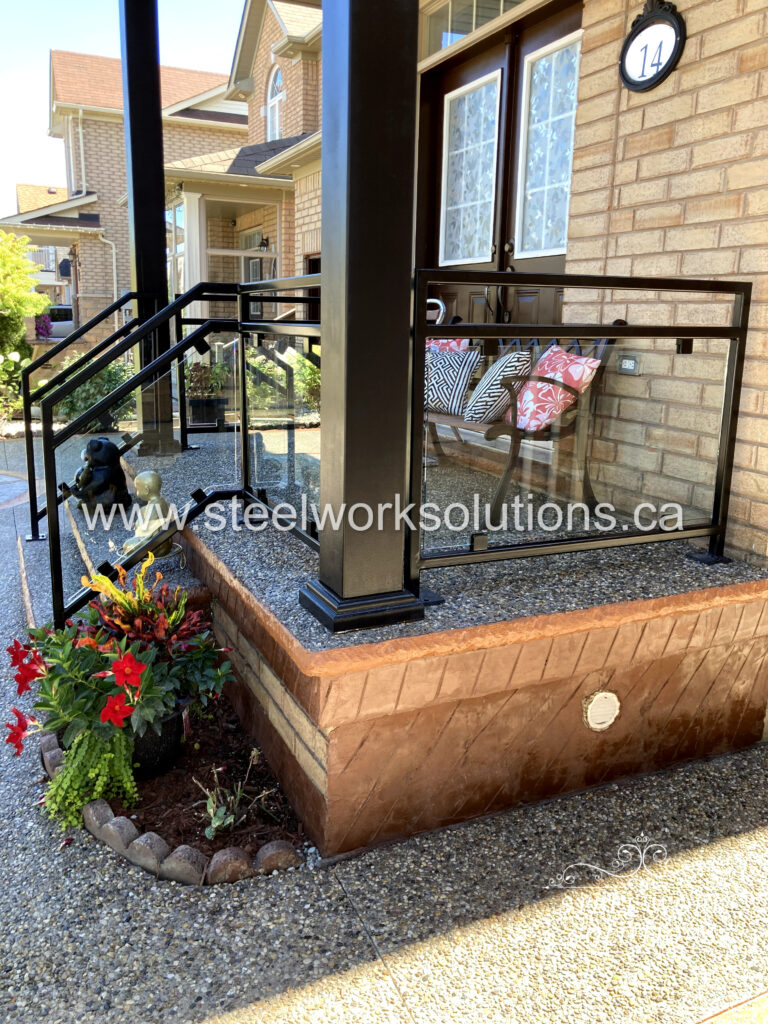
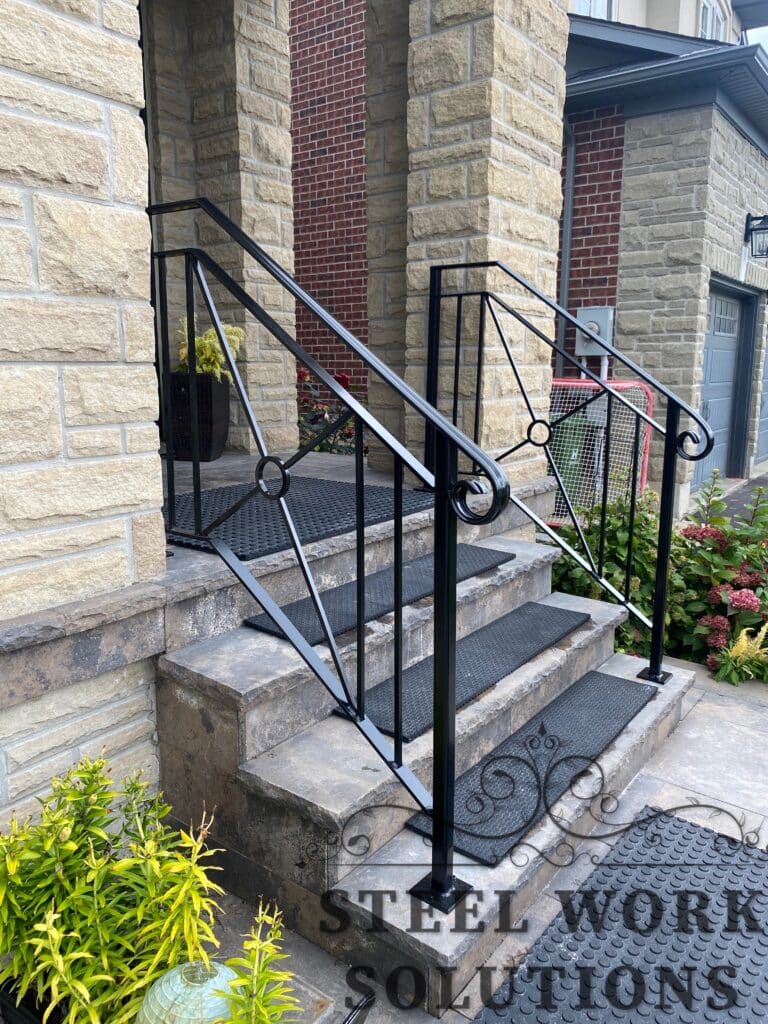
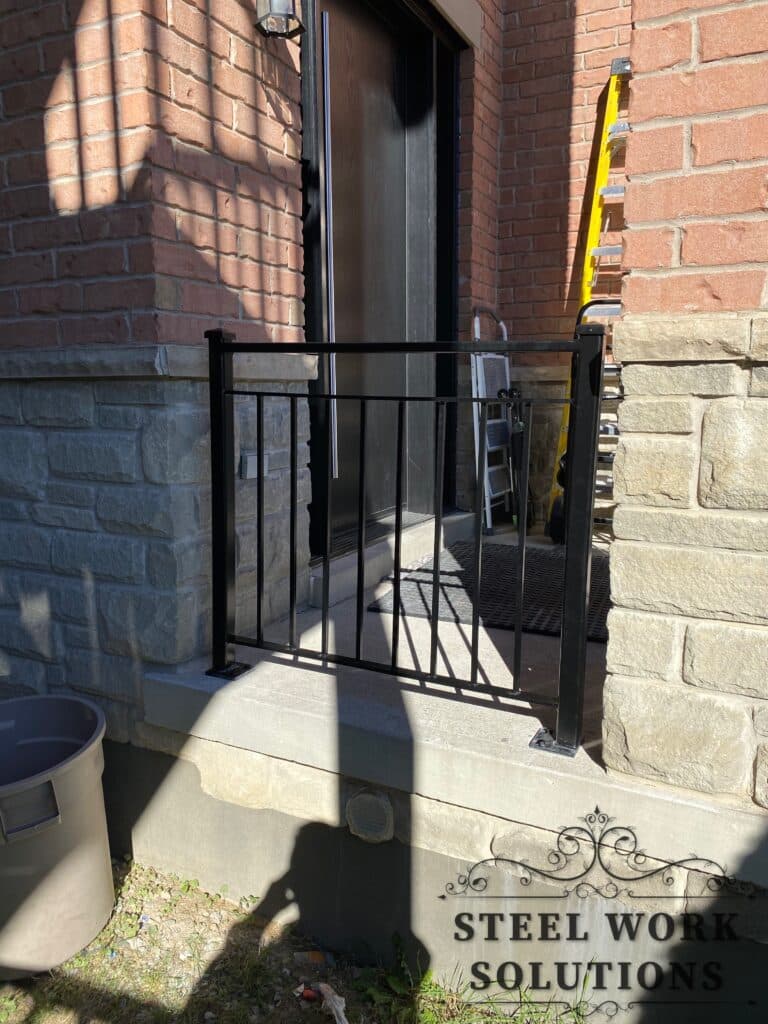
Advantages of Choosing Custom Aluminum Fabrication and TIG Welding
Opting for custom aluminum fabrication and TIG welding offers several distinct advantages:
1. Tailored Solutions:
Custom fabrication allows you to create products that are specifically designed to meet your needs, whether you require unique dimensions, specific features, or a particular aesthetic.
2. High-Quality Results:
The precision and control offered by TIG welding, combined with the versatility of aluminum, result in products that are not only functional but also high in quality and durability.
3. Cost-Effectiveness:
Although custom fabrication and TIG welding may have a higher upfront cost compared to standard options, the longevity and minimal maintenance required for aluminum products make them a cost-effective choice in the long run.
4. Enhanced Aesthetics:
Whether you’re looking for sleek, modern designs or more traditional styles, custom aluminum fabrication allows you to achieve the exact look you want, with welds that are clean and virtually invisible.
Conclusion
Custom aluminum fabrication and TIG welding represent the pinnacle of precision and quality in metalwork. Whether you’re in need of custom railings for your home, specialized parts for your business, or unique architectural features, this combination offers unparalleled results. By choosing custom aluminum fabrication and TIG welding, you’re investing in products that are tailored to your needs, built to last, and crafted to the highest standards of quality.
If you’re ready to explore the possibilities of custom aluminum fabrication and TIG welding for your next project, reach out to the experts at Steel Work Solution today. Our team of skilled professionals is here to help you bring your vision to life with precision, craftsmanship, and attention to detail.